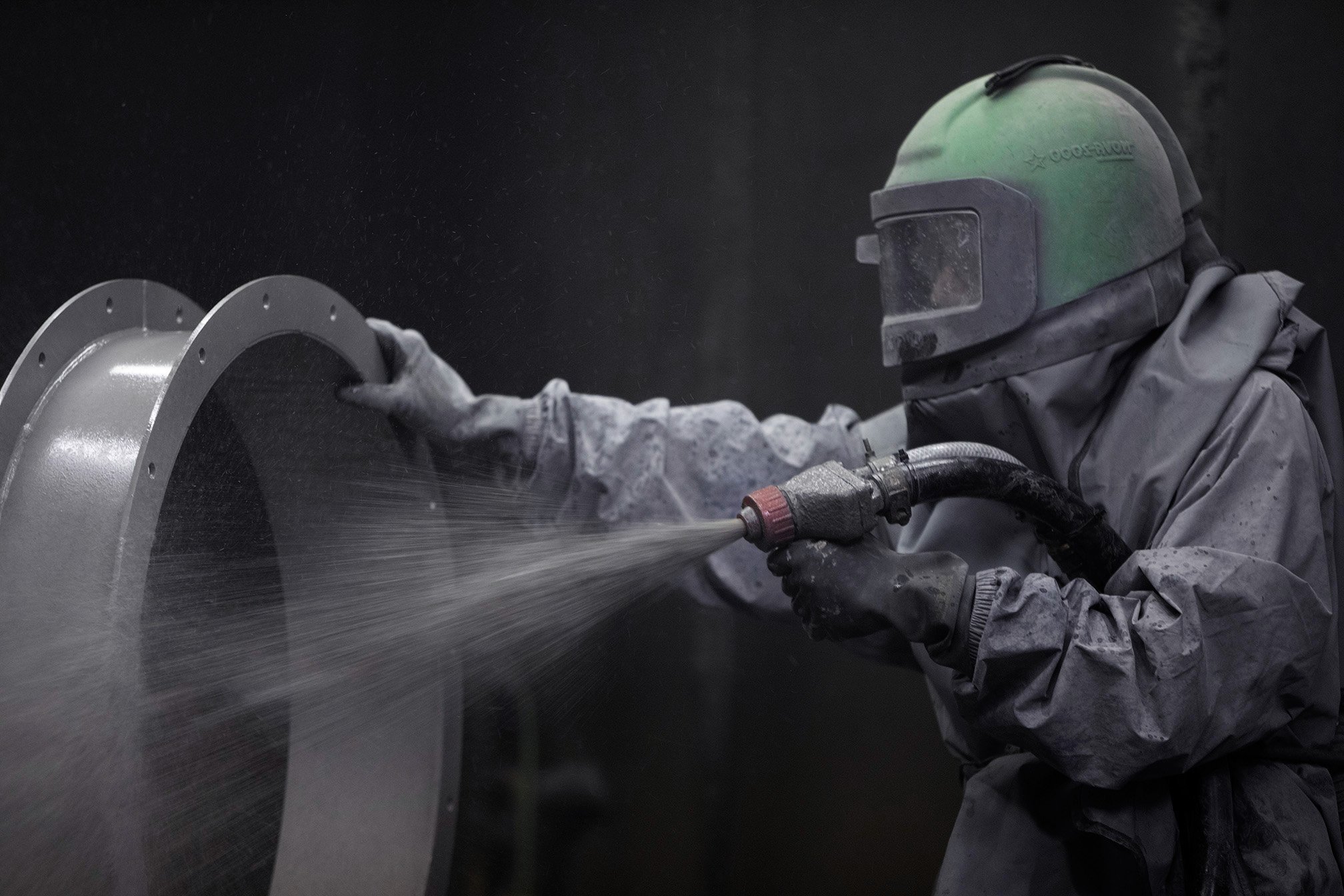
BEADBLASTING • AQUABLASTING • SHOTBLASTING • POWDER PAINT REMOVAL • PAINT AND RUST REMOVAL
Click to find out more.
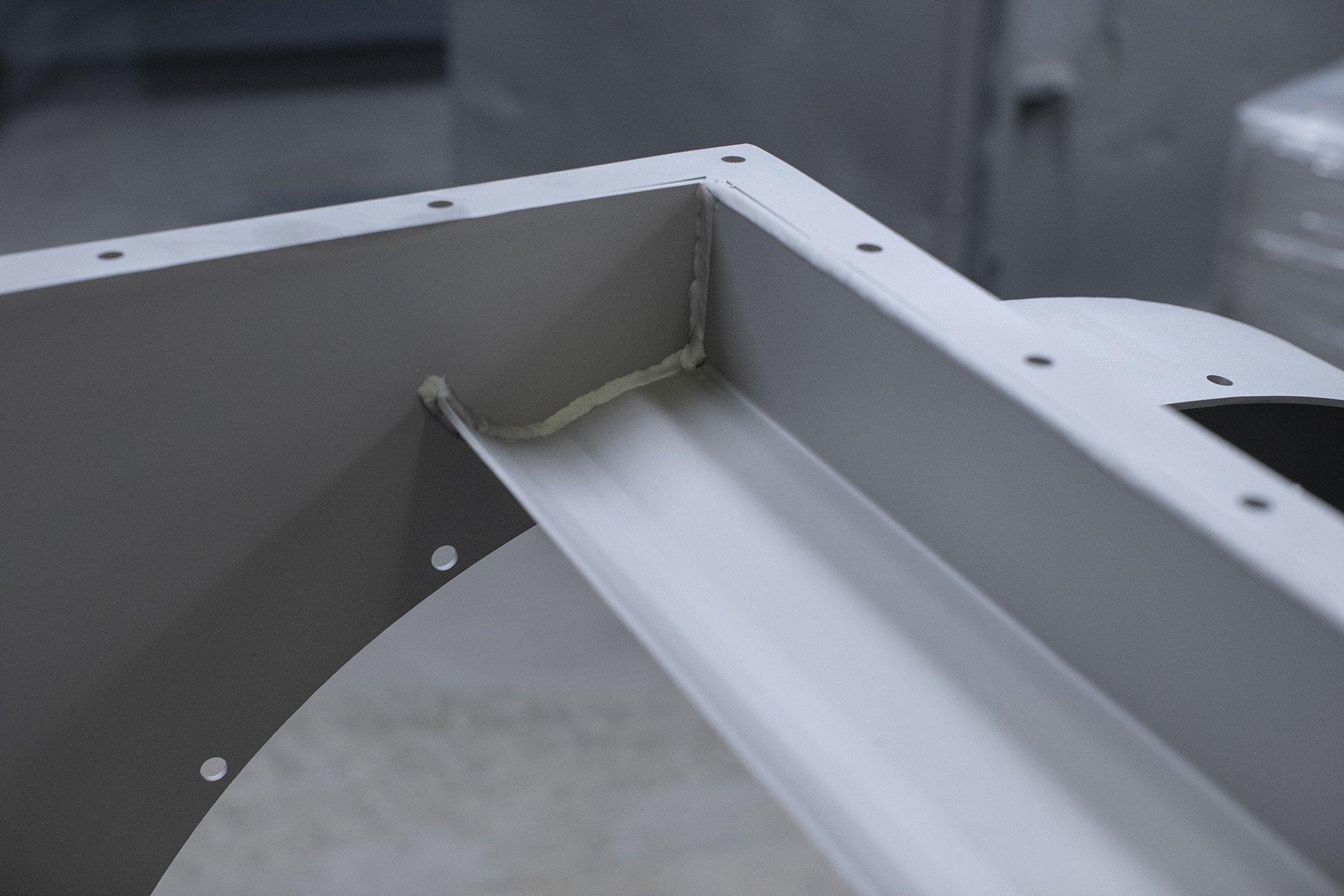
Using fine, nonmetallic abrasives in one of our three bespoke blasting chambers, our bead blasting services produce a perfectly clean and uniform finish on even the most awkward shapes.
For more information on our equipment and blasting standards, please contact us.
DISCOVER THE BENEFITS OF BEAD BLASTING:
A consistent finish every time.
No impingement of ferrous contamination into the surface.
No acid weeping from the joints and inside of box sections.
No accidental folding of the metal – this often occurs with heavy machine polishing.
We offer a range of different finishes that can be achieved on stainless steel:
STAGE 01
MATT
For an even finish, 1 stage bead blasting is done using a fine aluminum oxide. This produces a quality matt grey finish.
STAGE 02
SEMI SHEEN
We use a fine glass bead during the process of 2 stage bead blasting to give a bright and quality finish.
STAGE 03
SILKY
A very fine glass bead is used throughout the 3-stage process to get the best quality finish available.
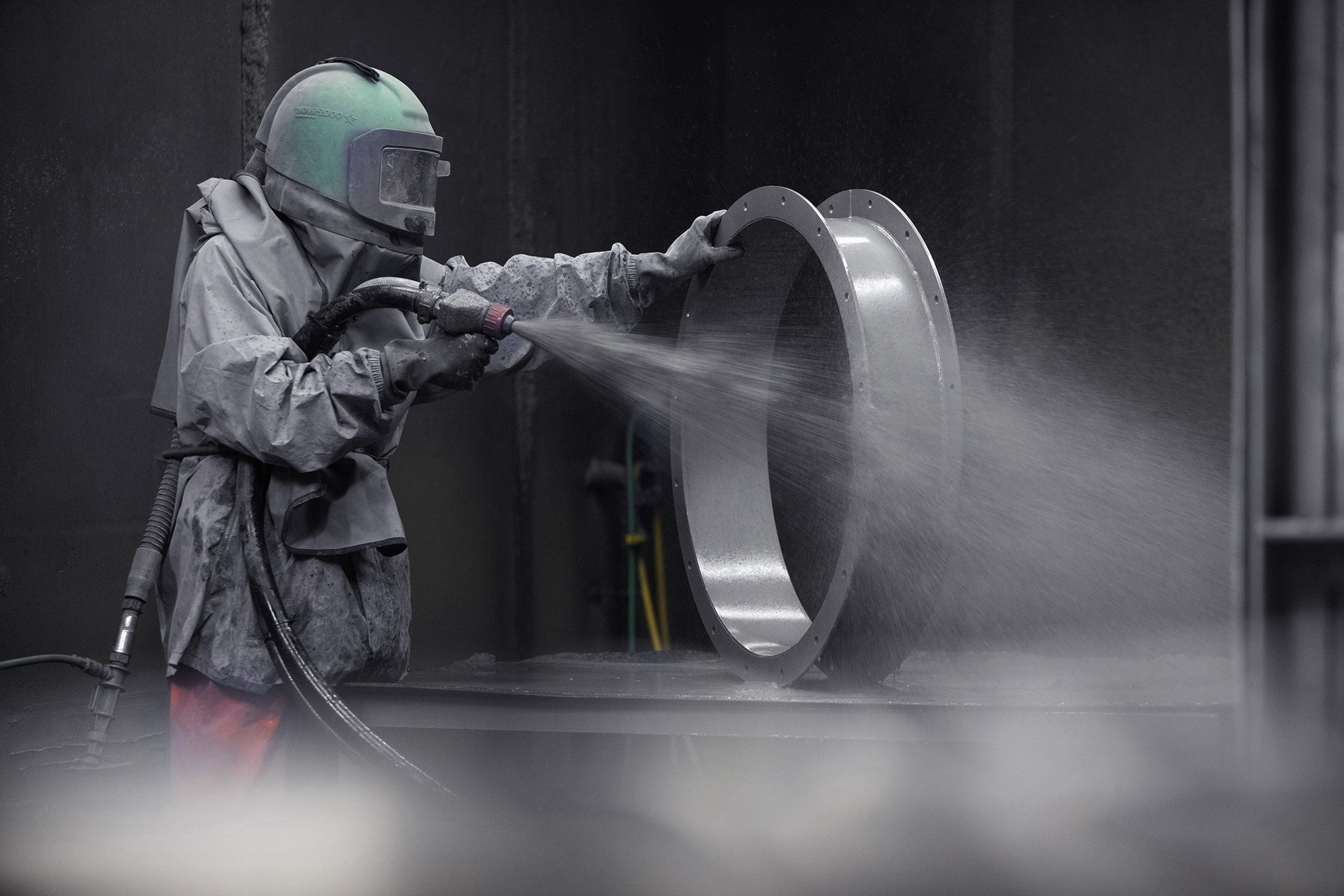
Aqua blasting, also known as Vapour blasting, is a method of blasting that uses a very fine media mixed with water. This surface impact treatment is for stainless steel and other non-ferrous metals. Aqua blasting leaves a high quality, easy wipe and stain resistant finish.
For more information on our equipment and blasting standards, please contact us.
DISCOVER THE BENEFITS OF AQUA BLASTING:
A consistent finish every time.
No impingement of ferrous contamination into the surface.
No acid weeping from the joints and inside of box sections.
No accidental folding of the metal – this often occurs with heavy machine polishing.
Aqua Blasting finishes include:
MATT VAPOUR BLAST
STANDARD VAPOUR BLAST
BRIGHT VAPOUR BLAST
For samples of the different finishes, please contact our expert Customer Service team on (+44) 01422 368758.
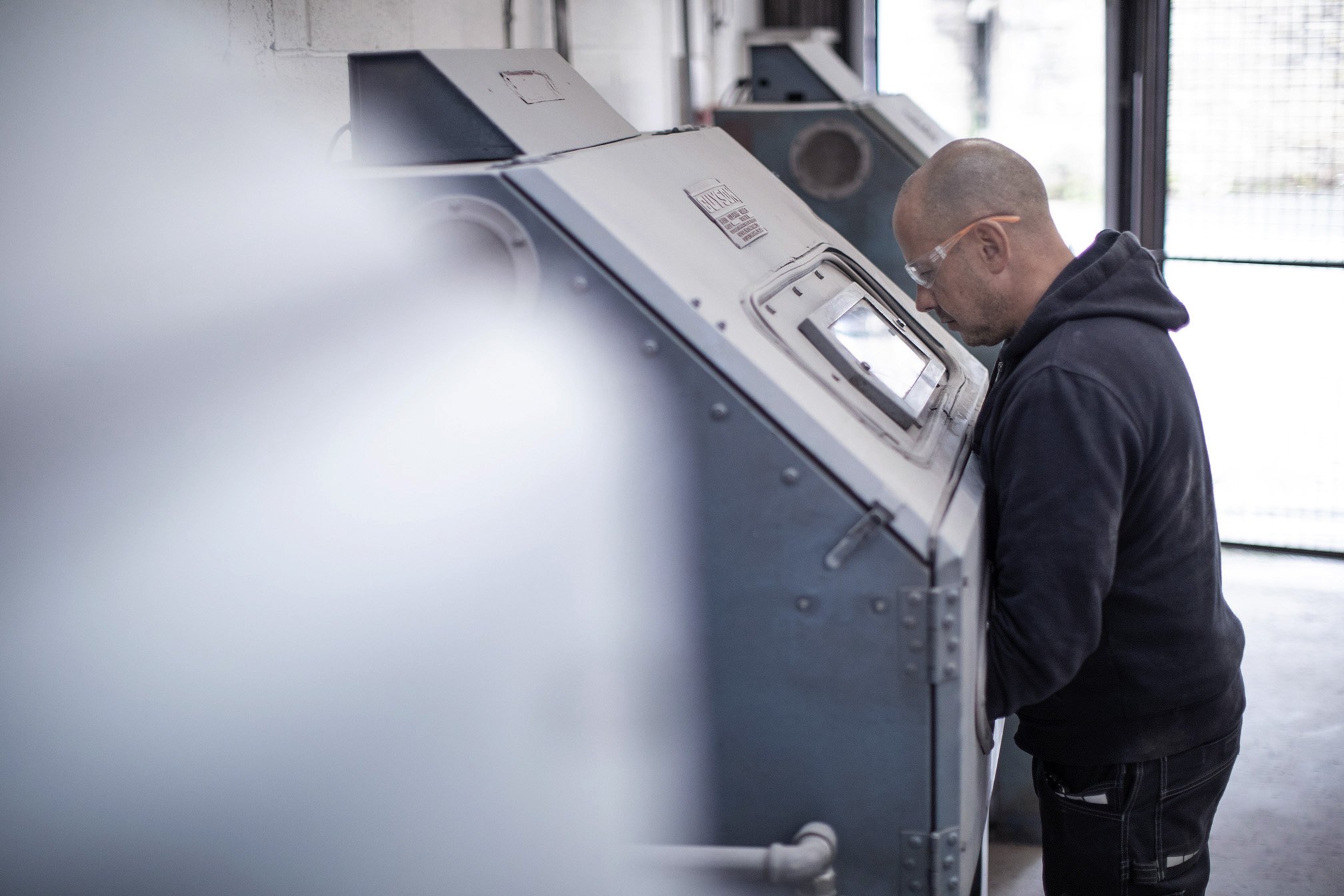
We use a process known as shot blasting to clean metals. Using a high-speed stream of ball shot and steel grit particles powered towards the object, we can thoroughly remove any previous paints, lacquers and surface rust so the metal is cleaned to bare white metal standards (SA2.5 – SA3).
The application of new paint or powder coatings can then bond to the clean surface of the metal.
We have a wide range of blasting facilities for all sized objects. No job is too big or small.
Our shot blasting facilities:
Manual blast rooms for larger objects
7.5M L x 3.5M W
Automatic Tumblast rubber belt machine for smaller objects
Automatic Centriblast barrel for larger batch blasting
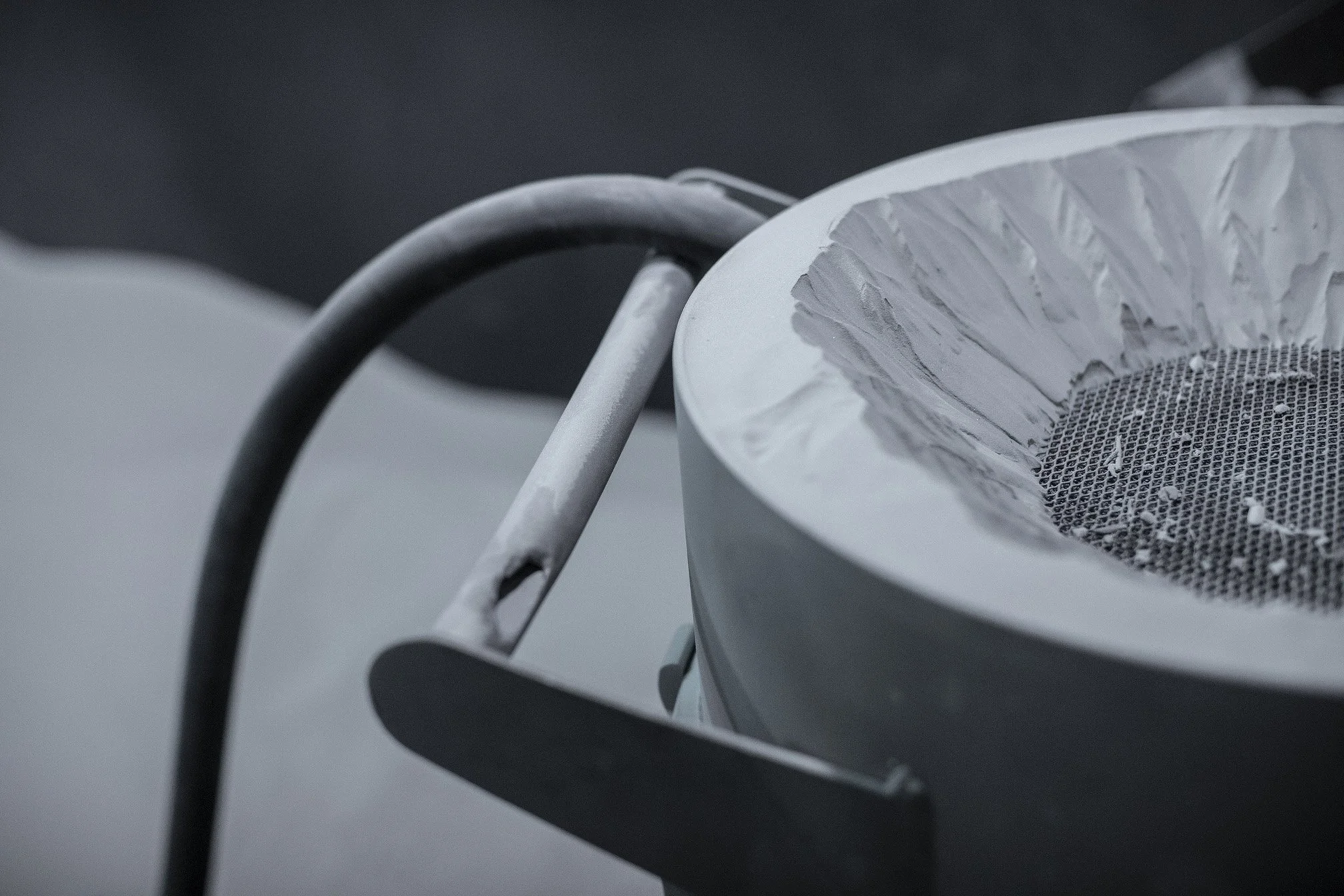
We remove paint and powders from metal using our large thermal controlled oven. The variable temperature control allows our experts to heat up or cool down the oven during the paint removal process to avoid damage to most materials.
The oven ensures an even heat distribution across the object and will reduce the powder coating or paint to ash.
*If required, we can apply a coat of weldable primer.
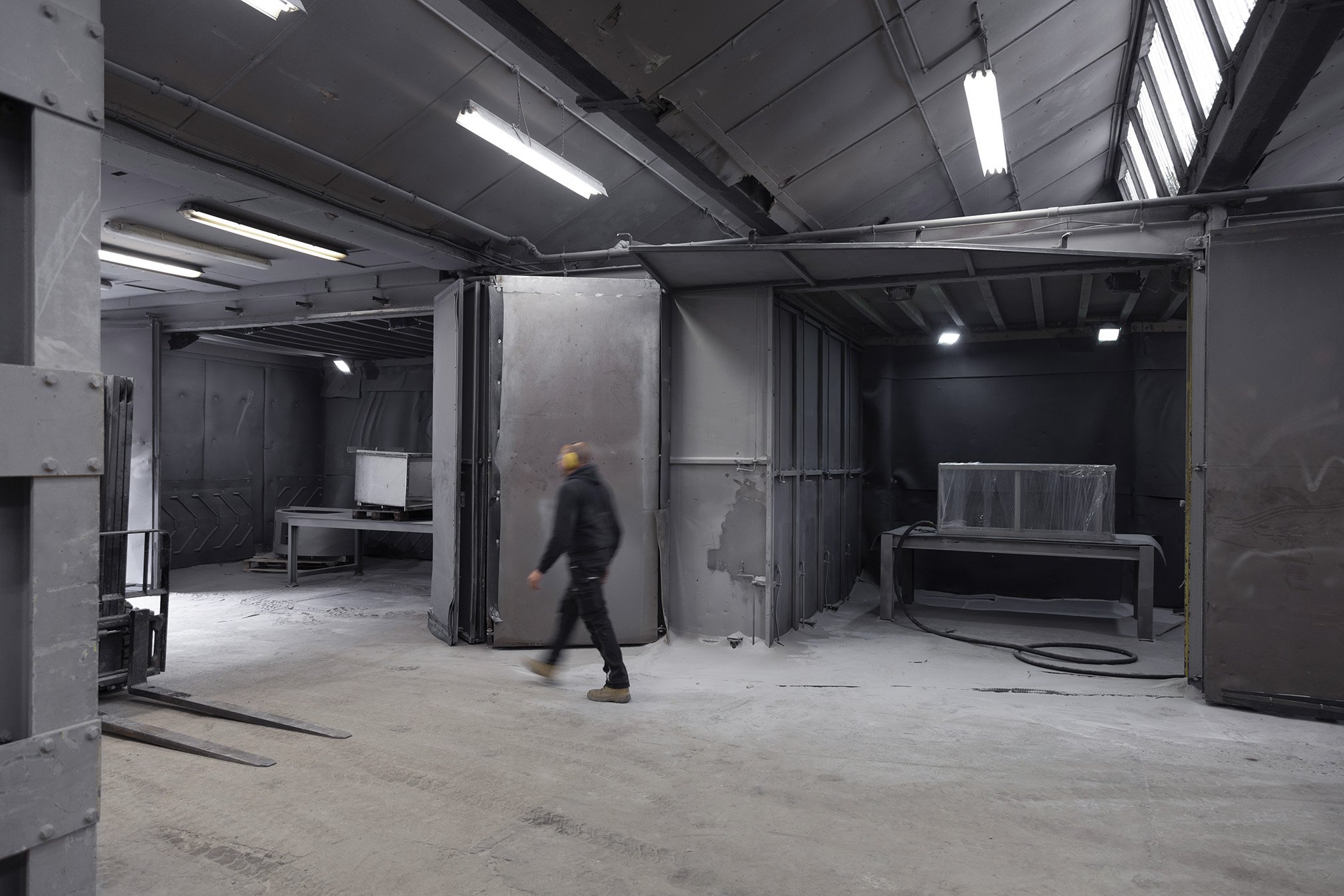
At BeadShot™, we specialise in removing paint, filler, rust and underseal from parts. We do this by baking the components in our temperature-controlled thermal oven to bake off the unwanted elements.
Following the baking process, [if required] we lightly blast the object at low air pressure with a fine aluminium oxide to remove any ashy residue.
Once the component has been completely cleaned, [if required] we apply a coat of zinc phosphate weldable blast primer to protect the bare white metal from the elements.
Note:
This method of removing paint, filler, rust and underseal is a ‘dry’ process. We do not use any acid or water.